How to setup siemens active Line Drive modules for SINAMICS S120 servo type modular?
Control Unit for SINAMICS S120:
It’s brain of Sinamics S120 drive systems. Whic is controllered Active Line module, Basic Line module and Linier line module. Interface and software programming stored is there and communication with each other’s drivers.
Line Module:
Key facts and benefits of BML, SLM, ALM:
- “Ready to run” operation solution to control an infeed system
- Tappet chain (pockets) or constant distance (without pockets) on outlet belt
- Automatic control and coordination of the belt movements
- Quick engineering just by parameterizing (without programming)
- Number of belts only limited by used CPU type
- Manual jog mode functionality
- Automatic check of technology object configuration
- Designed for call in LAD and easy diagnostics
- Contactless product handling
- How to setup siemens active Line Drive modules for SINAMICS S120 servo type modular?
Motor Module:
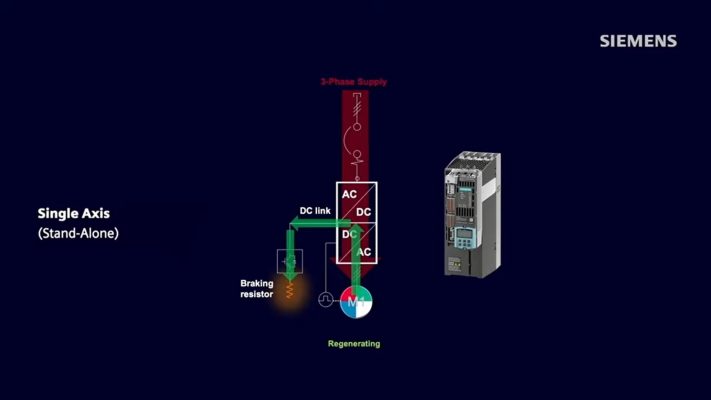
The Elongated Perspicacious Mode is not permissible for 12-pulse applications. Parameter p3533, “Infeed, inhibit regenerative operation”, can be acclimated to minimize. The reactive current in no-load operation in this operating mode as well. The regenerative direction in order to increment the robustness of performance may make sense even during motor operation if one or more of the following conditions apply.
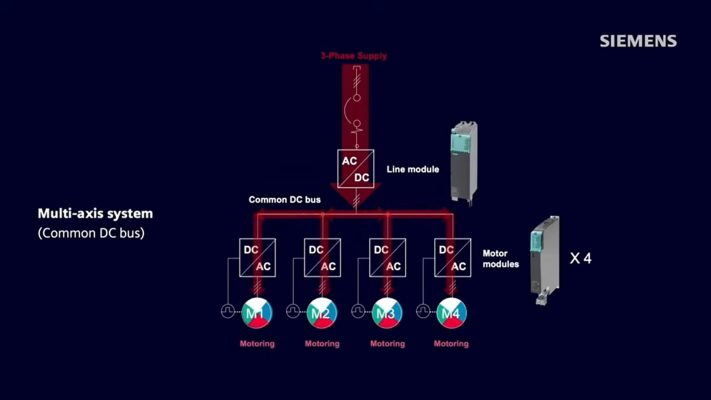
The Setup siemens active Line Drive modules for SINAMICS S120 servo type modular setup?
Basic Infeed of Line Module:
- Unregulated DC link voltage
- Control of external braking resistors with 20 kW and 40 kW
- Basic Line Modules (withtemperature monitoring)
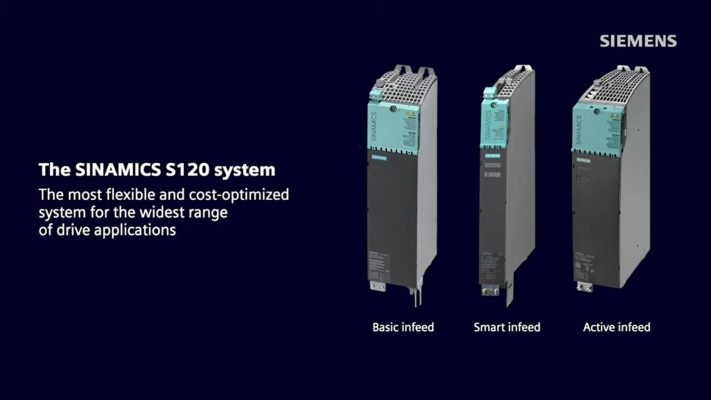
Smart infeed SINAMICS:
Smart infeed BLM:
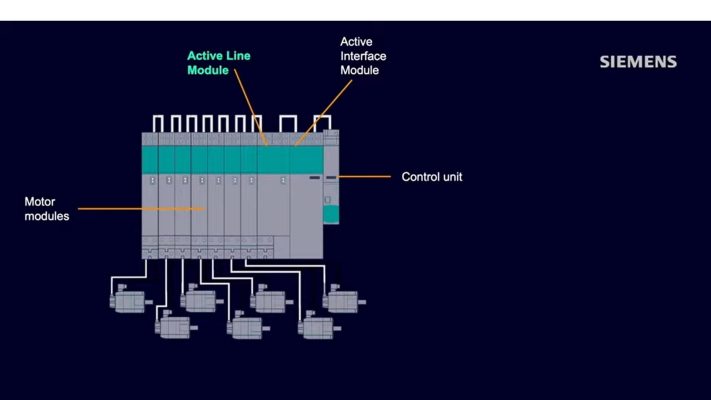
Active infeed Line Module:
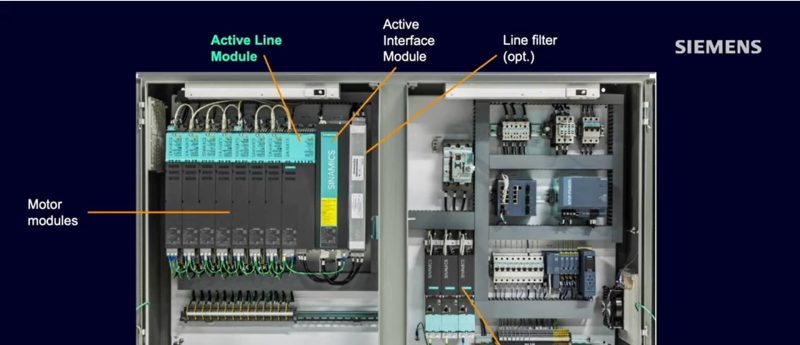
Basic Line Module (BLM):
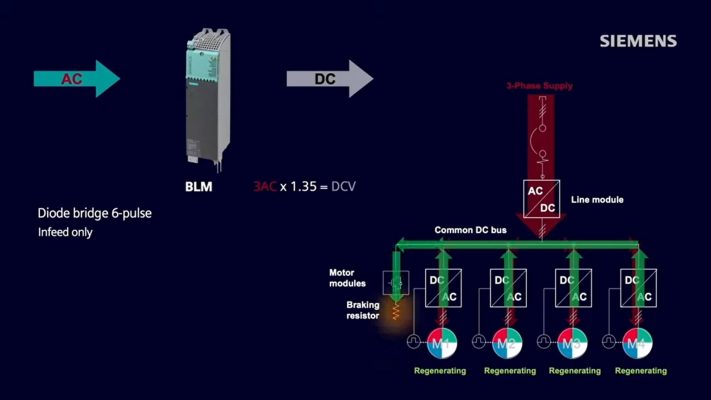
Siemens active Line Drive modules for SINAMICS S120 servo type modular?
Setting up Siemens Active Line Modules (ALM) for SINAMICS S120 servo drives involves several steps to ensure proper configuration and operation. Below are the general steps you would follow:
1. Hardware Setup
- Install ALM Modules: Physically mount the Active Line Modules in your cabinet according to the manufacturer’s instructions.
- Connect Power: Ensure that the ALM modules are connected to the appropriate power supply as specified in the module’s documentation.
- Connect to DC Bus: Connect the ALM modules to the DC bus of the SINAMICS S120 servo drive system.
2. Configuration in STARTER (Siemens Configuration Tool Software)
- Open STARTER: Launch the STARTER software on your PC.
- Identify Modules: Go to the Hardware Catalog and identify the ALM modules you have installed. Add them to your hardware configuration.
- Assign Parameters: Configure the parameters of the ALM modules. This may involve setting up communication parameters and addressing.
3. Configuration in SINAMICS Control Unit
- Access Drive Parameters: Connect to the SINAMICS control unit (via STARTER or other configuration tools) to access the drive parameters.
- Enable ALM Modules: Enable the Active Line Modules in the drive’s configuration settings. This typically involves setting the correct hardware configuration and enabling the ALM functions.
4. Testing and Commissioning
- Run Diagnostics: Use diagnostic tools within STARTER or the SINAMICS control software to verify that the ALM modules are communicating correctly and functioning properly.
- Test Operation: Run test operations to ensure that the ALM modules are providing. The desired benefits such as improved power quality and reduced harmonic distortion.
- Commissioning: Once all configurations are set and verified, proceed with the commissioning of the entire servo drive system.
5. Safety and Compliance
- Ensure Safety Standards: Always adhere to safety guidelines and regulations when configuring and operating servo drive systems.
- Compliance Check: Verify that the entire setup complies with local and international standards for electrical installations and servo drive systems.
Additional Tips:
- Consult Documentation: Refer to the specific manuals and documentation provided by Siemens for detailed instructions on configuring and setting up the ALM modules with SINAMICS S120 drives.
- Training and Support: If you are new to this setup, consider attending training sessions or consulting with Siemens support for assistance.
By following these steps and guidelines, you can effectively set up Siemens Active Line Modules for your SINAMICS S120 servo drive system, ensuring optimal performance and reliability.