PLC-HMI Inverter-VFD Sensor-encoder & controller for machine parts
For designing and integrating a complete automation solution involving PLCs, HMIs, inverters, VFDs, sensors, encoders, and controllers for machine parts, it’s essential to select components that work seamlessly together. Here’s an overview of each component, along with recommended products and their integration.
1. PLC (Programmable Logic Controller)
PLCs are central to industrial automation systems, controlling various processes and machinery.
- Recommended Brand: Siemens SIMATIC series
- Model: S7-1200 or S7-1500
- Features: High scalability, integrated IOs, robust network communication, and extensive diagnostic capabilities.
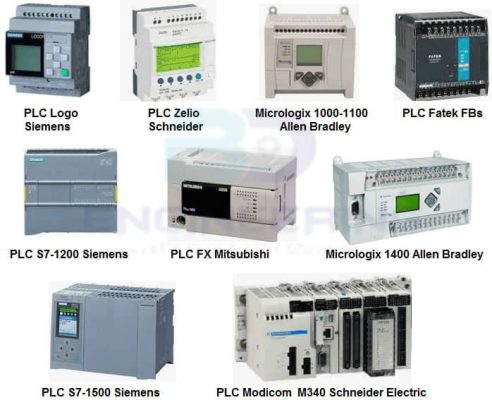
2. HMI (Human-Machine Interface)
HMIs allow operators to interact with the machine, providing control and monitoring capabilities.
- Recommended Brand: Siemens SIMATIC HMI
- Model: KTP700 Basic or TP700, TP900, TP1200, TP1500 Comfort
- Features: High resolution, touch screen interface, extensive communication options, and user-friendly design.
3. Inverter/VFD (Variable Frequency Drive)
Inverters and VFDs control the speed and torque of electric motors, enhancing efficiency and performance.
- Recommended Brand: Siemens SINAMICS series
- Model: SINAMICS G120
- Features: Modular design, integrated safety features, energy-efficient motor control, and easy integration with Siemens PLCs.
- delta Inverter-vfd MS300 & CP200, C200 vector control etc
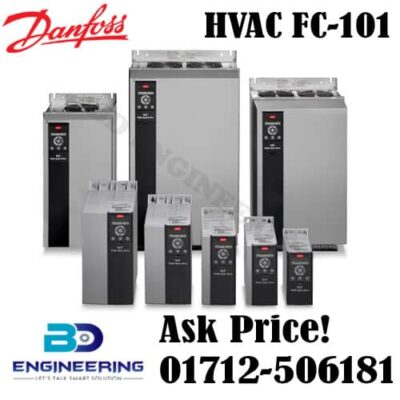
4. Sensor
Sensors provide critical data about the machine’s operating conditions, such as position, temperature, and pressure.
- Recommended Brand: Omron or SICK
- Model: Omron E3Z series for photoelectric sensors, SICK DT50 for distance sensors
- Features: High precision, reliability, and compatibility with various environments.
5. Encoder
Encoders provide precise feedback on the position and speed of a motor or other rotating equipment.
- Recommended Brand: Siemens or Heidenhain
- Model: Siemens 1XP8001 (incremental), Heidenhain ERN 1387 (absolute)
- Features: High resolution, robust design, and seamless integration with PLCs for precise control.
6. Controller
Controllers manage specific functions of a machine, often working in conjunction with PLCs for comprehensive control.
- Recommended Brand: Siemens SIMOTION or SIMATIC Controllers
- Model: SIMOTION D410 or SIMATIC ET 200SP
- Features: High performance, real-time control, and advanced motion control capabilities.
Integration and Software
Siemens TIA Portal
- Description: The Totally Integrated Automation (TIA) Portal is Siemens’ engineering framework, providing an integrated environment for programming and configuring PLCs, HMIs, drives, and other automation components.
- Benefits: Simplifies engineering tasks, reduces configuration times, enhances productivity, and ensures seamless integration between all Siemens components.
Typical Workflow for Integration
- Design and Specification:
- Determine the requirements of the machine, including the number of IOs, types of sensors, and motor specifications.
- Choose the appropriate PLC model (e.g., S7-1200 for small to medium applications).
- Programming:
- Use TIA Portal to program the PLC, configure the HMI interface, and set up communication protocols.
- Implement logic for motor control, data acquisition from sensors, and user interactions via HMI.
- Hardware Setup:
- Install the PLC, HMI, inverters/VFDs, sensors, and encoders.
- Ensure proper wiring and connections according to the design specifications.
- Testing and Commissioning:
- Test each component individually, then integrate and test the entire system.
- Use the TIA Portal’s diagnostic tools to troubleshoot and optimize the system.
- Maintenance and Monitoring:
- Utilize HMI for real-time monitoring and control.
- Implement predictive maintenance strategies using sensor data and diagnostic information.
Example Components for a Machine Automation Setup
- PLC: Siemens S7-1500
- HMI: Siemens TP700 Comfort
- Inverter/VFD: Siemens SINAMICS G120
- Sensor: Omron E3Z-D82 (photoelectric sensor)
- Encoder: Heidenhain ERN 1387
- Controller: Siemens SIMATIC ET 200SP
Encoders are devices used to convert motion into an electronic signal that can be interpreted by a control system. They are commonly used in various applications, including robotics, industrial machinery, and automated systems. There are two primary types of encoders: incremental and absolute encoders. Each type has its distinct characteristics and uses. Here’s a detailed comparison:
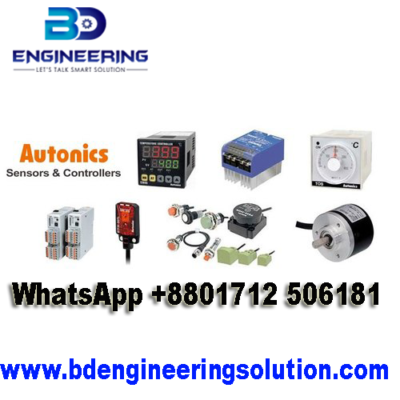
Incremental Encoders
How They Work
- Signal Output: Incremental encoders generate pulses as the encoder shaft rotates. Each pulse corresponds to a specific increment of movement.
- Relative Positioning: They measure the relative change in position. The position is determined by counting the number of pulses from a reference point.
- Index Pulse: Many incremental encoders have an index pulse (Z-pulse) that occurs once per revolution, serving as a reference point to reset the position counter.
Advantages
- Simplicity: Incremental encoders are generally simpler in design and easier to integrate.
- Cost-Effective: They tend to be less expensive than absolute encoders.
- High Resolution: Capable of providing high resolution and precise measurement of motion.
Disadvantages
- Loss of Position on Power Down: If the system loses power or the encoder signal is interrupted, the exact position is lost, and the system must be re-referenced.
- Cumulative Error: Errors can accumulate over time if pulses are missed or if there is electrical noise.
Applications
- Speed Control: Ideal for applications where only speed or relative movement needs to be measured.
- Position Tracking: Used in CNC machines, robotics, and other applications where high precision relative position tracking is required.
Absolute Encoders
How They Work
- Signal Output: Absolute encoders provide a unique digital code (usually binary or gray code) for each distinct position of the shaft. This code represents the absolute position.
- Absolute Positioning: They measure the absolute position directly, meaning the exact position is always known, even after a power cycle.
Advantages
- No Re-referencing Required: After a power loss, the exact position is immediately known without the need for re-referencing.
- Error-Free Positioning: No cumulative errors because each position is unique and does not rely on previous positions.
Disadvantages
- Complexity: Absolute encoders are more complex in design and integration.
- Cost: They are generally more expensive than incremental encoders.
- Lower Resolution: For a given physical size, absolute encoders may have lower resolution compared to incremental encoders due to the complexity of generating a unique code for each position.
Applications
- Position Control: Used in applications requiring exact positioning, such as robotics arms, servo motors, and precise automation systems.
- Safety-Critical Systems: Essential in systems where knowing the exact position at all times is critical, such as in medical devices and aerospace.
Comparison Summary
Feature | Incremental Encoder | Absolute Encoder |
Position Measurement | Relative | Absolute |
Power Loss Recovery | Requires re-referencing | Immediate position available |
Complexity | Simpler | More complex |
Cost | Generally lower | Generally higher |
Resolution | Typically higher for the same size | Typically lower for the same size |
Applications | Speed control, relative position tracking | Precise position control, safety-critical systems |
A sensor is a device or component that detects changes in its environment and converts those changes into measurable signals or data. Sensors are fundamental elements in various systems, from everyday consumer electronics to complex industrial machinery. They play a crucial role in collecting data for monitoring, control, and automation purposes. Here’s a breakdown of key aspects of sensors:
Functionality:
- Detection: Sensors detect changes or events in their surroundings, such as temperature, pressure, light, motion, or the presence of certain substances.
- Transduction: They convert the detected physical quantity into an electrical, optical, or other measurable signal.
- Output: The output signal can be analog (continuous) or digital (discrete), depending on the sensor type and application.
- Interface: Sensors often interface with other components, such as microcontrollers, processors, or control systems, to process and act upon the collected data.
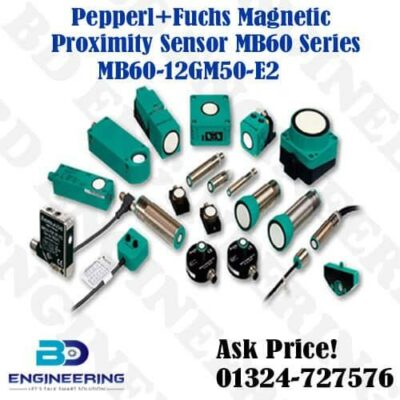
Types of Sensors:
- Temperature Sensors: Measure temperature changes.
- Pressure Sensors: Detect changes in pressure levels.
- Proximity Sensors: Sense the presence or absence of nearby objects.
- Motion Sensors: Detect movement or changes in position.
- Light Sensors: Measure light intensity or detect light presence.
- Humidity Sensors: Monitor humidity levels in the environment.
- Gas Sensors: Detect the presence and concentration of gases.
- Biometric Sensors: Measure biological parameters, such as heart rate or fingerprints.
Characteristics:
- Accuracy: The degree of conformity between the sensor’s output and the actual value being measured.
- Sensitivity: The ability to detect small changes in the measured quantity.
- Range: The range of values within which the sensor can accurately measure.
- Resolution: The smallest change in the measured quantity that the sensor can detect.
- Response Time: The time it takes for the sensor to detect a change and provide a corresponding output.
- Robustness: The sensor’s ability to withstand environmental factors such as temperature variations, humidity, and mechanical stress.
Applications:
- Automotive: Used in vehicle systems for engine management, airbag deployment, and parking assistance.
- Industrial Automation: Employed in manufacturing processes for quality control, monitoring, and predictive maintenance.
- Consumer Electronics: Found in smartphones, wearables, and smart home devices for various sensing functions.
- Environmental Monitoring: Utilized for weather forecasting, air quality monitoring, and pollution detection.
- Medical Devices: Used for patient monitoring, diagnostic equipment, and drug delivery systems.
Conclusion:
Sensors are vital components in modern technology, enabling the collection of data for analysis, control, and decision-making. Their versatility and wide-ranging applications make them indispensable in numerous industries and everyday devices, contributing to advancements in efficiency, safety, and quality of life.