SICK Motor Feedback Encoder SRS50-HWA0-K21
The SICK SRS50-HWA0-K21 is a motor feedback encoder designed to provide precise and reliable position and speed feedback for motor control applications. This encoder is part of the SICK SRS50 series, which is known for its robust construction, high accuracy, and suitability for industrial environments.
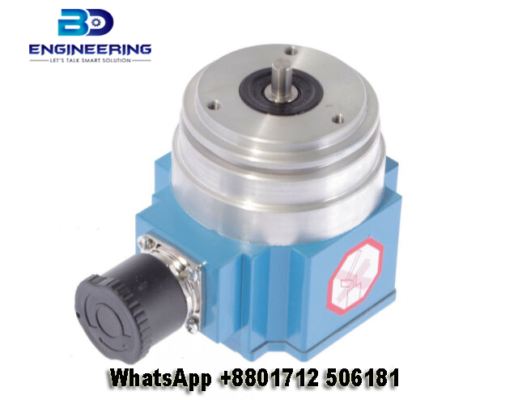
Key Features of SICK SRS50-HWA0-K21 Motor Feedback Encoder:
- Mechanical Design:
- Housing: Compact and robust housing designed for industrial applications.
- Mounting: Flange mounting with various options to fit different motor configurations.
- Shaft: Solid shaft design with specified diameter for direct coupling to the motor.
- Performance:
- Resolution: Provides high-resolution feedback for precise motor control. The exact resolution can vary, so refer to the product datasheet for specific values.
- Accuracy: High accuracy in position and speed feedback, ensuring reliable motor control.
- Speed: Capable of handling high rotational speeds, suitable for dynamic applications.
- Electrical Interface:
- Output Signals: Incremental encoder with standard output signals such as A, B, and Z channels. These signals are used for position and speed feedback.
- Supply Voltage: Operates typically on 5V or 24V DC, depending on the specific model configuration.
- Connection: Standard connectors or cables for integration with motor controllers and drive systems.
- Environmental Specifications:
- Temperature Range: Designed to operate in a wide temperature range, making it suitable for various industrial environments.
- Protection Rating: High IP rating (e.g., IP65), providing resistance to dust and moisture.
- Compatibility:
- Integration: Compatible with various motor drives and controllers, making it versatile for different industrial applications.
- Feedback Systems: Suitable for use with servo motors, stepper motors, and other applications requiring precise feedback.
Installation and Usage:
- Mounting: Ensure the encoder is mounted securely using the flange and mounting hardware. Align the encoder shaft correctly with the motor shaft to avoid mechanical stress and ensure accurate feedback.
- Wiring: Connect the encoder’s output signals (A, B, Z channels) to the corresponding inputs on the motor controller or drive. Ensure proper grounding and shielding of cables to minimize electrical noise and interference.
Applications to Industry:
- Industrial Automation: Position and speed feedback for CNC machines, robotic arms, and automated assembly lines.
- Material Handling: Precise control of conveyor systems, lifts, and sorting mechanisms.
- Textile Machinery: Feedback for weaving, knitting, and other textile production processes.
- Printing Industry: Position control for printing presses and cutting machines.
- Packaging: Accurate feedback for packaging machinery, ensuring precise operation.
We have extensive experience in a wide range of industries and processes and require products with intelligent sensors. We can deliver exactly what our customers need. In application motor feedback rotary types of machinery. SICK Motor Feedback Encoder SRS50-HWA0-K21