What is redundant & redundancy in Automation Engineering method
In Automation engineering, redundancy refers to the including of extra components or devices with a system that are not strictly necessary for functionality. But serve as a backup in case of failure the control systems. This practice is the reliability, safety, and availability by ensuring that a system can continue to operate and functional even if part of its failures.
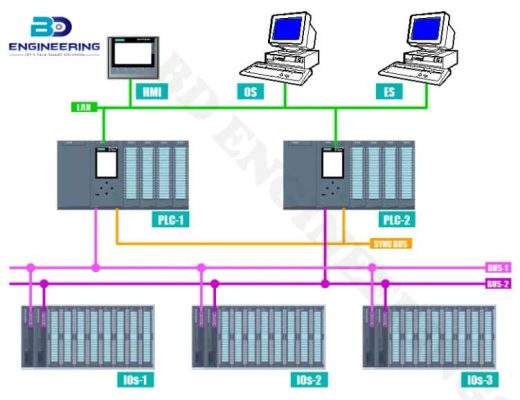
Types of Automation Redundancy:
- Component or devices Redundancy: Adding extra individual components like plc and power supply with control devices
- System Control Redundancy: Including complete backup systems like dual servers or duplicate data centers stations
- Functional Redundancy systems: Designing systems to have multiple ways of performing the same function as like different routes in the network
- Information Redundancy: Storing extra information to detect and correct errors like to parity bits in data storage to media.
Redundancy in Automation Engineering:
There have Redundancy in automation engineering refers to the inclusion of backup components or systems within a process to ensure uninterrupted operation even in case of failures or malfunctions operation. It’s a critical concept for building robust and reliable automation systems.
Benefits of Redundancy:
- Save Cost: Implementing redundancy increases costs.
- Complexity & easy solution: More components can lead to increased complexity and potential points of failure.
- Easy Maintenance: More systems require more maintenance and monitoring.
- Redundancy is a fundamental: The concept in engineering design, balancing reliability and cost to meet the desired performance and safety standards.
- Increased Uptime: Redundancy significantly reduces downtime by minimizing the impact of component failures.
- Enhanced Reliability: Critical systems with redundancy are more likely to operate continuously without interruptions.
- Improved Safety: In safety-critical applications, redundancy can prevent catastrophic failures and ensure the safety of personnel and equipment.
- Data Integrity redundant & redundancy in Automation Engineering method is a very easy operation
Practical Example of redundant PLCs:
- In the manufacturing plant, having redundant PLCs and I/O modules, and network switches can be ensured that is production line keeps running even if one component fails. This prevents costly downtime and production losses.
- By carefully considering the critical components and software development of an automation system and implementing appropriate redundancy measures, it’s possible to achieve high levels of system.
Hardware Redundancy:
- Dual Controllers Devices: Employing two identical controllers for critical tasks, with one acting as a hot standby while the other is active.
- Redundant I/O Modules: Using to multiple I/O modules for critical inputs and outputs to ensure data integrity and system operation even if one module fails.
- Power Supply Redundancy: Having dual power supplies or uninterruptible power supplies (UPS) to maintain system operation during power outages or fluctuations.
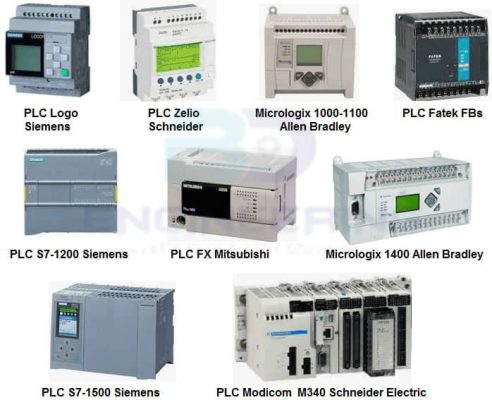
Functional Redundancy area
- Diversity: Using different technologies or components for the same function to reduce the likelihood of simultaneous failures. For example, using both pneumatic and hydraulic systems for a braking mechanism.
- Voting Systems: Employing multiple sensors or actuators to provide redundant data or control signals. The system makes decisions based on a majority vote among these components.
Challenges and Considerations
- Cost: Redundancy can increase initial investment due to additional hardware and software requirements.
- Complexity: Implementing and maintaining redundant systems requires careful planning and expertise.
- False Positives: Redundancy systems might trigger false alarms, requiring proper configuration and testing to minimize false positives.
- Performance Impact: In some cases, redundancy can introduce slight performance overhead due to the need for communication and synchronization between redundant components.
Case Studies and Examples:
- Automotive Power Plant: Redundant PLCs and I/O modules to ensure continuous power plant in case of component failures. Mostly important of continues production line of manufacturing
- Process Control systems: The Redundant sensors, actuators, and controllers to maintain critical process parameters and prevent safety hazard issues.
- Inverter-VFD redundant Systems: Most of company make sure of redundant functionalities VFD_Inverter for various application
Practical Implementation of Redundancy:
I/O Redundant
- Dual I/O Modules: Employing two identical I/O modules for critical inputs and outputs. Data from both modules is compared, and discrepancies are flagged or corrected.
- Remote I/O: Distributing I/O modules across multiple locations to reduce the impact of a single point of failure.
Network Redundancy:
- Ring Topology: Creating a closed-loop network where data can be transmitted in both directions, improving fault tolerance.
- Redundant Switches: Using multiple switches to provide alternative communication paths.
- Industrial PC: Offering higher reliability application for both application continues runing that can use IPC systems control panel.
Power Supply Redundant:
- Dual Power Supplies: Employing two separate power supplies to ensure continuous operation even if one fails.
- Uninterruptible Power Supplies (UPS): Providing backup power during power outages.
Automotive Assembly Line:
- Redundant PLCs: Two identical PLCs control critical assembly processes, with one acting as a hot standby.
- Redundant I/O Modules: Critical sensors and actuators are connected to dual I/O modules to prevent production stops due to I/O failures.
- Redundant Network: A ring topology network with multiple switches ensures uninterrupted communication.
Oil and Gas Platform utilities area:
- Dual system Controllers: Two identical PLCs control safety-critical functions like emergency shutdown systems with utilities operation area.
- Redundant Sensors: Critical sensors like pressure and temperature sensors have multiple units for cross-checking input data systems.
- Uninterruptible Power Supplies (UPS): UPS systems provide backup power to critical equipment during power outages.
Challenges and Optimization controllers:
- Cost-Benefit Analysis: Evaluate the potential financial impact of system downtime versus the cost of implementing redundancy systems automation development
- Testing and Validation: Thoroughly test the redundant system to ensure proper operation and failover mechanisms.
- Complexity Management: Simplify the system design to avoid excessive complexity that can hinder troubleshooting and maintenance.
- Dynamic Reconfiguration: Explore options for automatically reconfiguring the system in case of failures to minimize downtime.
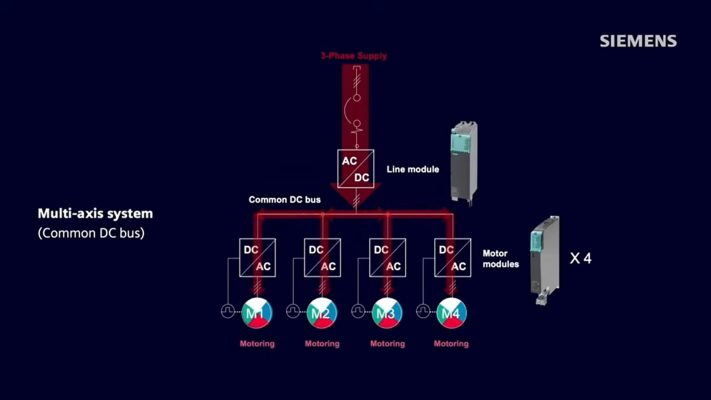
Standby redundancy in the PLCs concepts:
- Hot to Standby:
- Two PLCs are continuously online and synchronized.
- One PLC is active, while the other is in a standby mode continues, monitoring the primary for failures.
- Upon failure detection, the standby PLC takes over seamlessly, ensuring minimal downtime.
- Warm to Standby:
-
- Similar to hot standby, but the standby PLC might not be fully synchronized with the primary.
- It might require some time to synchronize or load programs after taking over, resulting in a slightly longer recovery time.
- This option is suitable for applications where short interruptions are tolerable.
- Cold to Standby:
-
- The standby PLC is completely offline until the primary fails.
- Manual intervention is required to bring the standby online, leading to longer recovery times.
- This option is suitable for non-critical systems where downtime can be planned.
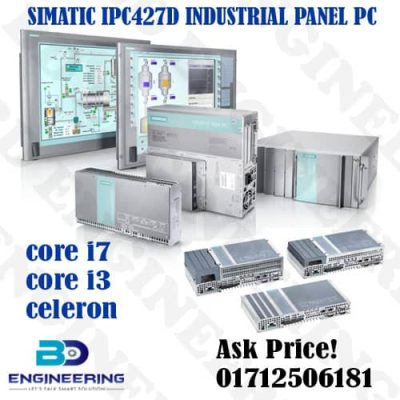
Redundancy in I/O Systems of PLC controller
- Dual I/O Modules: Employing two identical I/O modules for critical inputs and outputs. Data from both modules is compared, and discrepancies are flagged or corrected.
- Remote I/O: Distributing I/O modules across multiple locations to reduce the impact of a single point of failure.
Network Redundancy topology:
- Ring-Topology: Creates a closed-loop network where data can be transmitted in both directions.
- Redundant Switches: Using multiple switches to provide alternative communication paths.
- Fiber Optic Cables area: Offers higher reliability and resistance to electromagnetic interference compared to copper cables.