Rotary Encoder Supplier Company in BD
A rotary encoder is an electromechanical device used to convert the angular position or motion of a rotating shaft into an electrical signal. It provides feedback on the position, speed, and direction of rotation of a rotating object, such as a motor shaft or a mechanical component.
- Baumer Encoder:
Rotary encoders typically consist of a rotating shaft, a disk or a code wheel attached to the shaft, and sensors to detect the movement of the disk. There are two main types of rotary encoders: incremental and absolute.
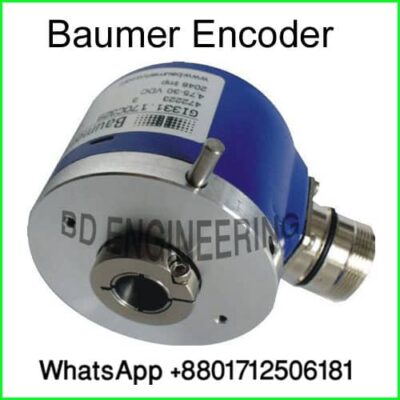
- Incremental Rotary Encoder:
An incremental encoder generates a series of pulses as the shaft rotates. These pulses are typically in the form of two output signals, namely A and B channels (also known as quadrature signals). The A and B channels are 90 degrees out of phase, which allows determining both the position and the direction of rotation. By counting the number of pulses and their direction, the relative position and speed of the shaft can be determined.
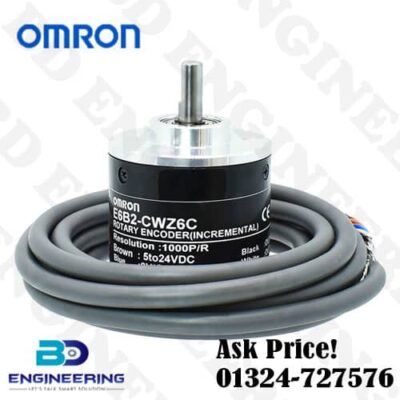
- Absolute Rotary Encoder:
An absolute encoder provides a unique binary or digital code for each position of the shaft within a full rotation. This means that the encoder can directly indicate the absolute position of the shaft without the need for counting pulses. Absolute encoders are often used when accurate position feedback is required, even if power is lost or the system is restarted.
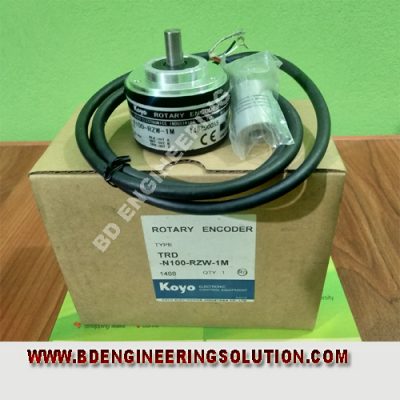
- Autonics Encoder:
Rotary encoders can also have additional features such as index pulses, which provide a reference point or a start/end position for a complete rotation. They may also have resolutions, which determine the number of pulses or codes generated per revolution, and can range from a few pulses to thousands or more, depending on the specific application.
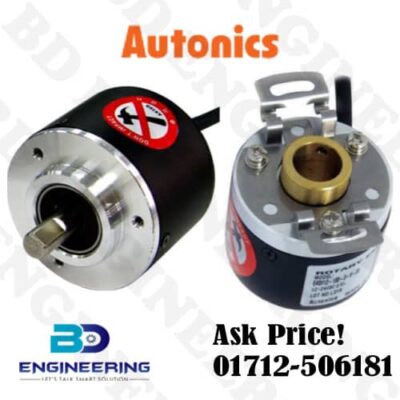
- SICK Encoder:
Rotary encoders are widely used in various industries and applications, including robotics, CNC machines, industrial automation, motion control systems, and digital control panels.
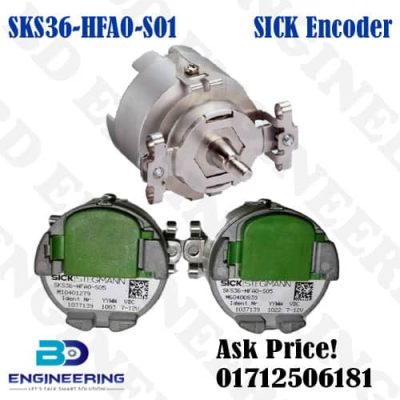
- Koyo Encoder:
They provide essential feedback for controlling and monitoring rotational movements, enabling precise positioning, speed control, and synchronization of mechanical components and processes.