Supply Incremental & absolute Encoder with resolver
It looks like you are looking for encoders and resolvers for motion control applications. Provides position feedback by generating pulses as the shaft rotates. Provides a unique position value for each shaft position, making it ideal for applications where position needs to be known immediately upon power-up.
What is the Absolute Encoder?
Absolute encoders measure absolute or veridical angular position control. This contrasts with incremental encoders which quantification the vicissitude in angular position. The test as to whether an encoder is absolute or incremental is what transpires at power up. If the encoder has to move or go through some ‘wake and shake’ process to determine its position then it is incremental. If it outputs its veridical position without kineticism then it is absolute. The absolute position feedback, meaning it knows its exact position even after power cycles.
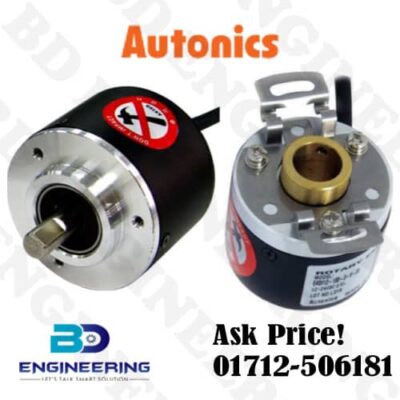
What is the Resolver?
A analog position sensor that provides absolute position feedback using sinusoidal signals to output. An electromechanical device that provides analog signals proportional to the shaft’s angular position.
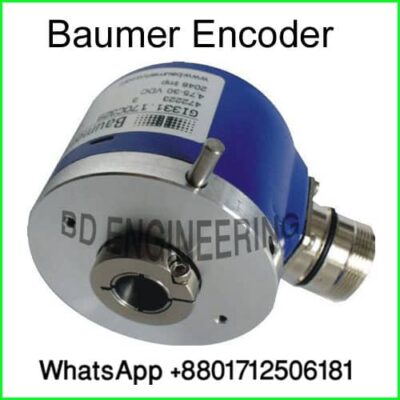
What is the Incremental Encoder?
Provides precise position feedback by counting pulses generated as the shaft rotates. An incremental encoder is a type of encoder contrivance that converts angular kineticism or position of a shaft into an analog or digital code to identify position or kineticism. Incremental encoders are one of the most commonly used rotary encoders.
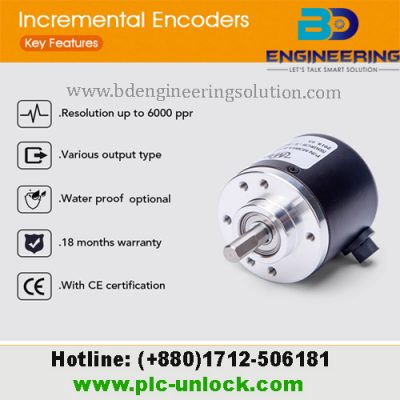
Combine These Technologies?
Incremental encoders provide high resolution for precise motion control, while absolute encoders ensure accurate position information even after power loss. The combination can provide redundancy, improving system reliability. If one feedback system fails the other can still provide position information. Combining the strengths of different technologies.
Typical Applications Center?
Used in applications requiring precise motion control, such as robotics, machine tools, and aerospace. Resolver TS2651N141E78 TAMAGAWA Encoder for Servo Motor
Key Considerations:
- Cost: Combining these technologies can increase the overall cost of the system.
- Complexity: Integrating and calibrating multiple feedback systems can add complexity to the system design.
- Space Constraints: Combining multiple sensors may require additional space within the system.
Recommendations to use as below brands:
- Siemens, Neimicon, Renishaw, Heidenhain, Tamagawa, Baumer, Sick, Omron, Dynapar, Rockwell Automation.
- Optical or magnetic encoders with quadrature (A/B) and optional index pulse.
- Brushless resolvers, pancake resolvers, and geared resolvers for heavy-duty applications.
- To specific model based on resolution, communication protocol, or environmental requirements.